فرمولاسیون چسب پنچرگیری به صورت مایع و یا چسبندهای است که برای پنچرگیری لاستیکهای موتور، دوچرخه و خودرو استفاده میشود.
برای تولید چسب پنچرگیری، از موادی همچون لاتکس، رزین، کربنات کلسیم، آمونیاک، آب و… استفاده میشود.
به طور کلی، چسب پنچرگیری یا چسب مایع ضد پنچری برای جلوگیری از به وجود آوردن خسارت های وارد شده به تایر و سایر وسایل نقلیه طراحی شده است. فرمولاسیون چسب پنچرگیری ممکن است بسته به نوع لاستیک و سایر عوامل متفاوت باشد.
برای تولید چسب پنچرگیری، مواد افزودنی های مختلفی مانند رقیق کننده ها، دیسپرس کننده ها، یراق کننده ها، لیزر کننده ها،
مات کننده ها، بهبود دهنده خواص جریان پذیری، خشک کننده ها، پایدارکننده توری، ضدباکتری ها و ضد حریق ها ممکن است استفاده شوند.
جهت کسب اطلاعات بیشتر میتوانید در سایت فرمول 3 از مقاله های دیگر نیز بازدید بفرمایید.
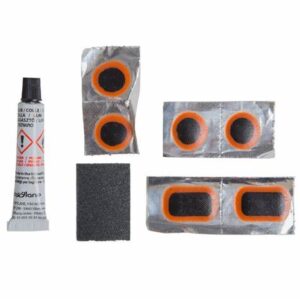
برای تولید چسب پنچرگیری، شما نیاز به تجهیزات و مواد اولیه زیر دارید:
- لاتکس: لاتکس یک ماده مایع است که به عنوان پایه چسب پنچرگیری استفاده میشود.
- رزین: رزینها به عنوان یک ماده چسبنده در فرمولاسیون چسب پنچرگیری استفاده میشوند.
- کربنات کلسیم: کربنات کلسیم به عنوان یک ماده پرکننده در فرمولاسیون چسب پنچرگیری استفاده میشود.
- آمونیاک: آمونیاک به عنوان یک ماده شستشو در فرمولاسیون چسب پنچرگیری استفاده میشود.
- آب: آب برای تقویت و رقیق کردن فرمولاسیون چسب پنچرگیری استفاده میشود.
تذکر: تولید چسب پنچرگیری نیاز به دانش و تجربه خاصی دارد.
برای تولید این چسب، شما باید دقت کافی را در اندازهگیری و ترکیب مواد داشته باشید.
همچنین، باید از تجهیزات ایمن و مناسب برای کار با مواد شیمیایی استفاده کنید.
لطفاً توجه داشته باشید که تولید و استفاده از محصولات شیمیایی باید با دقت و با رعایت اصول ایمنی صورت گیرد.
در صورت عدم آشنایی کافی با فرآیند تولید، بهتر است از خرید چسب پنچرگیری آماده استفاده کنید.
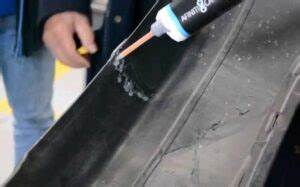
برای استفاده از چسب پنچرگیری، مراحل زیر را دنبال کنید:
- آمادهسازی: قبل از استفاده از چسب پنچرگیری، لاستیک را به طور کامل تمیز کنید و از وجود هر گونه ذرات خارجی مطمئن شوید.
- استفاده از چسب: چسب پنچرگیری را به طور مستقیم روی سطح لاستیک بمالید.
در صورت لزوم، میتوانید از یک قطعه پارچه تمیز برای پخش بهتر چسب استفاده کنید.
- خشک کردن: بعد از مالیدن چسب، آن را به خوبی خشک کنید. زمان لازم برای خشک شدن چسب ممکن است بسته به نوع آن متفاوت باشد.
- آزمایش: پس از خشک شدن چسب، لاستیک را باد کنید و از عملکرد چسب پنچرگیری در حالت واقعی مطمئن شوید.
لطفاً توجه داشته باشید که هر چسب پنچرگیری ممکن است دارای دستورالعملهای خاص خود باشد.
برای بهترین نتایج، همیشه دستورالعملهای تولید کننده را مطالعه کنید و به طور صحیح عمل کنید.
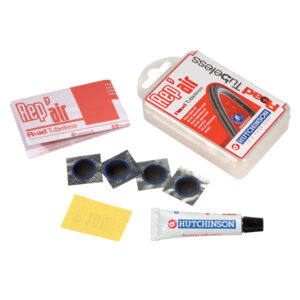
استفاده از چسب پنچرگیری، مزایای زیادی دارد. چسب پنچرگیری، به صورت مایعی است که قبل از سوراخ شدن تایر وسایل نقلیه ریخته میشود، و هنگام سوراخ شدن لاستیک بلافاصله محل سوراخ را پر میکند.
برخی از مزایای استفاده از چسب پنچرگیری عبارتند از:
- رفع دائم پنچری: چسب پنچرگیری، به صورت دائمی سوراخ لاستیک را پوشش میدهد و از خروج باد جلوگیری میکند.
- افزایش عمر مفید لاستیک: استفاده از چسب پنچرگیری، باعث افزایش عمر مفید لاستیک میشود.
- مانع از زنگ زدگی و پوسیدگی داخل رینگ: چسب پنچرگیری، حاوی ترکیبات ضد زنگ است و از پوسیدگی و زنگ زدگی رینگ ها جلوگیری میکند.
- مانع از یخ زدگی در هوای خیلی سرد: وجود چسب پنچرگیری در لاستیک، از یخ زدگی در هوای خیلی سرد جلوگیری میکند.
- حفاظت از لاستيك در برابر حرارت: چسب پنچر گيري جنوب، حرارت را به درستي انتقال ميدهد بنابراین لاستيك را خنك نگهمیدارد.
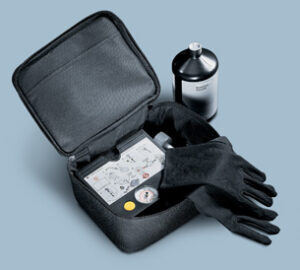
استفاده از چسب پنچرگیری، همانند هر محصول شیمیایی دیگری، ممکن است دارای معایبی باشد.
برخی از معایب استفاده از چسب پنچرگیری عبارتند از:
- تعمیر دائمی نیست: چسب پنچرگیری، تعمیر دائمی برای لاستیکها فراهم نمیکند و در برخی موارد، نیاز به تعویض لاستیک را احساس میکنید.
- تأثیر بر روی تعادل خودرو: استفاده از چسب پنچرگیری، ممکن است تأثیرات منفی بر روی تعادل خودرو داشته باشد.
- تأثیر بر روی عمر لاستیک: استفاده از چسب پنچرگیری، در مواردی ممکن است عمر لاستیک را کوتاه کند.
- تأثیر بر روی سلامت کاربر: استفاده از چسب پنچرگیری، ممکن است به سلامت کاربر آسیب بزند. در صورت تماس با چسب پنچرگیری، فوراً با آب و صابون ناحیه مربوطه خودتان را بشویید و به پزشک مراجعه کنید.
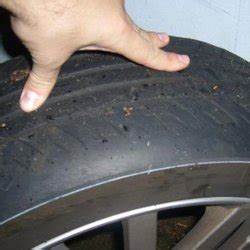
این اختراع مربوط به یک لاتکس بر پایه لاستیک مصنوعی سیس-1،4-پلی ایزوپرن (که از این پس به اختصار IR نامیده می شود) است. به طور خاص، اختراع مربوط به یک لاتکس نوع IR است که استحکام ژل مرطوب و استحکام لایه خشک را به طور قابل ملاحظه ای بهبود می بخشد و دارای ثبات و فرآیند پذیری عالی است.
2. شرح هنر قبلی
در این هنر به خوبی شناخته شده است که یک لاتکس IR زمانی به دست می آید که یک محلول IR تهیه شده با پلیمریزاسیون محلول ایزوپرن در حضور یک کاتالیزور نوع زیگلر یا یک کاتالیزور نوع لیتیوم ابتدا امولسیون شده و با کمک یک در آب پراکنده شود. عامل امولسیون کننده و سپس حلال با یا بدون غلظت بعدی از لاتکس رقیق حاصل حذف می شود. به عنوان مثال، US Pat را ببینید. شماره 3,285,869. با این حال، تولید لاتکس IR با روشهایی مانند موارد فوق، از این منظر که مقادیر زیادی از منعقدات پلیمری تمایل به ته نشین شدن در طی جداسازی، یعنی حذف حلال، یا در مرحله تغلیظ که در آن لاتکس رقیق است، رسوب میکند، مضر است. به عنوان مثال، با سانتریفیوژ متمرکز می شود. در نتیجه، چنین لاتکس IR به طور جدی در پایداری مکانیکی و حرارتی دچار کمبود است. پایداری مکانیکی و حرارتی ناکافی لاتکس مادون قرمز نه تنها مسئول مشکلاتی است که در تولید لاتکس تجربه میشود، بلکه یکی از دلایل اصلی مشکلات مختلفی است که وقتی لاتکس متعاقباً به محصولات لاستیکی شکلدار تبدیل میشود، با آن مواجه میشود. به عنوان مثال، انعقاد لاتکس با افزودن یک عامل ولکانیز کننده و سایر عوامل ترکیب کننده تحت هم زدن و همچنین در طول حمل و نقل لاتکس صورت می گیرد.
اگرچه استفاده از یک عامل امولسیون کننده در مقادیر قابل توجهی پایداری لاتکس را بهبود می بخشد، اما به طور قابل توجهی از خواص فیزیکی لاتکس از جمله استحکام ژل مرطوب، خاصیت تشکیل فیلم و استحکام لایه خشک آن می کاهد.
صرف نظر از اینکه مقدار قابل توجهی از عامل امولسیون کننده استفاده می شود یا خیر، لاتکس IR ذاتاً از لاتکس طبیعی در استحکام ژل مرطوب و استحکام فیلم خشک پایین تر است. استحکام ژل مرطوب به طور کلی به عنوان قدرت یک لاتکس اندازه گیری شده در طول انعقاد، یعنی قدرت لایه در نقطه ژل شدن مرطوب تعریف می شود. از طرف دیگر، استحکام فیلم خشک به عنوان استحکام فیلمی تعریف میشود که در آن انعقاد لاتکس کامل است و فاقد محیط مایع است. کاهش سطح استحکام ژل مرطوب و استحکام لایه خشک یک لاتکس منجر به کمبودهای جبران ناپذیری در محصولات لاستیکی مختلف تولید شده از لاتکس می شود. به عنوان مثال، در ساخت اقلام لاستیکی مانند دستکش و کالاهای پزشکی و بهداشتی با فرآیند غوطه وری، رگه ها و شیارهایی بر روی سطح فیلم از پوشش لاتکس روی قالب محدب ایجاد می شود و تغییر شکل فیلم رخ می دهد. وقتی از قالب خارج شد. چنین مشکلاتی که در بالا ذکر شد اغلب در فرآیند پردازش اقلام شکلی رخ می دهد که منجر به تولید محصولات رضایت بخش نمی شود. علاوه بر این، در تولید لاستیک فوم شده از چنین لاتکسی، با عیوب اضافی مانند پارگی میانی مواجه می شود که به دلیل استحکام ناکافی ژل مرطوب لاتکس است.
همانطور که قبلا ذکر شد، لاتکس IR دارای معایب ذاتی جدی است، به عنوان مثال، نقص در پایداری مکانیکی که عامل مهمی در تهیه و قالبگیری لاتکس و در استحکام ژل مرطوب، استحکام لایه خشک است، که هر دو تعیینکنندههای مهم خواص شکلدهی هستند. محصولات مشتق شده از لاتکس و اختراع حاضر به منظور بهبود لاتکس IR است.
خلاصه اختراع
بنابراین، هدف از اختراع حاضر ارائه یک لاتکس لاستیکی مصنوعی جدید از نوع cis-1،4-polyisoprene است که معایب فوق الذکر را ندارد.
هدف دیگر ارائه یک لاتکس لاستیکی مصنوعی از نوع cis-1،4-polyisoprene است که دارای درجه بالایی از پایداری مکانیکی است و استحکام ژل مرطوب و استحکام لایه خشک بهتری را در مقایسه با لاتکس لاستیک طبیعی نشان میدهد.
مطابق با اختراع حاضر، موارد فوق با تهیه یک لاتکس لاستیک مصنوعی مشتق شده از لاستیک پلی ایزوپرن مصنوعی حاصل از امولسیون کردن محلول لاستیک پلی ایزوپرن در یک حلال آلی با آب و حذف حلال از روغن در آب حاصل می شود. امولسیون، مشخصه لاتکس لاستیک مصنوعی این است که لاستیک پلی ایزوپرن مذکور یک لاستیک پلی ایزوپرن اصلاح شده است که با وارد کردن گروه های کربوکسیل به لاستیک مصنوعی سیس-1،4-پلی ایزوپرن به مقداری که لاستیک پلی ایزوپرن اصلاح شده حاوی 0.03 تا 20 گروه کربوکسیل باشد، تهیه شده است. واحدهای تکرارشونده مونومر ایزوپرن موجود در لاستیک پلی ایزوپرن مذکور (که از این پس به لاستیک اصلاح شده IR اصلاح شده نیز گفته می شود).
شرح مفصل اختراع
IR اصلاحشده طبق اختراع ممکن است با هر روش دلخواه تهیه شود، مشروط بر اینکه گروههای کربوکسی از این طریق به یک سیس-1،4-پلیسوپرن مصنوعی از قبل آماده شده وارد شوند.
فرآیند کلی و پارامترهای کاتالیزور برای پلیمریزاسیون ایزوپرن در یک محیط حلال هیدروکربنی آلیفاتیک یا آلی حلقوی در این هنر به خوبی شناخته شده است. کاتالیزورهای تولید سیس-1،4-پلی ایزوپرن بالا ممکن است به عنوان کاتالیزورهای نوع Ziegler و کاتالیزورهای آنیونی طبقه بندی شوند. کاتالیزورهای نوع زیگلر ترجیحاً از یک ترکیب آلی آلومینیوم و یک تتراهالید تیتانیوم تهیه می شوند و واکنش پلیمریزاسیون معمولاً با تماس ایزوپرن با کاتالیزور مذکور در محیط حلال هیدروکربنی در دمایی بین حدود 0 درجه سانتی گراد انجام می شود. تا 150 درجه سانتیگراد نمونه هایی از این ترکیبات آلی آلومینیوم عبارتند از تری متیل آلومینیوم، تری اتیل آلومینیوم، تری ایزو بوتیل آلومینیوم، آلومینیوم تری-n-بوتیل، آلومینیوم تری-n-پنتیل، آلومینیوم تری ایزواکتیل و آلومینیوم تری سیکلوهگزیل. با توجه به تتراهالید تیتانیوم، تتراکلرید تیتانیوم ارجح است. کاتالیزورهای آنیونی معمولی برای تولید IR شامل کاتالیزورهای مبتنی بر لیتیوم هستند که حاوی ترکیبات لیتیوم و/یا لیتیوم هستند. از جمله کاتالیزورهای شناخته شده مبتنی بر لیتیوم، می توان به فلز لیتیوم، لیتیوم هیدروکربیل و آمیدهای آلی لیتیوم اشاره کرد. در میان گونه های کاتالیزور ارجح تر، ترکیبات آلکیل لیتیوم مانند n-butyl lithium sec.-butyl lithium، amyl lithium و isobutyl lithium ذکر شده است. با این حال، هر کاتالیزور نوع زیگلر یا کاتالیزور آنیونی که برای پلیمریزاسیون محلول ایزوپرن مفید است، میتواند طبق این اختراع مورد استفاده قرار گیرد، و در نظر گرفته نشده است که فرآیند موضوع به هیچ وجه به دلیل هیچ پارامتر کاتالیزوری محدود شود.
گروه کربوکسیل فوق ممکن است به شکل نمک فلز قلیایی مانند نمک لیتیوم، سدیم یا پتاسیم باشد. در کربوکسیلاسیون، IR ممکن است قبل از تهیه لاتکس یا در طی تهیه آن کربوکسیله شود. بنابراین، عامل کربوکسیل کننده مورد استفاده لزوماً نیازی به داشتن یک گروه کربوکسیل آزاد ندارد، بلکه فقط باید گروهی داشته باشد که پس از هیدرولیز یا سایر تیمارهای بعدی پس از واکنش با IR، قابل تبدیل به یک گروه کربوکسیل (شامل نمک آن) باشد. برای راحتی، IR که با چنین عامل کربوکسیلهکننده قابل تبدیل واکنش داده است، از این پس به طور خلاصه به عنوان IR اصلاحشده نامیده میشود. روشهای معرفی گروههای کربوکسیل به IR و عوامل کربوکسیلهکنندهای که برای آنها استفاده میشوند به خودی خود شناخته شدهاند (بهعنوان مثال، US Pat. No. 2,662,874). دسته اول از عوامل کربوکسیله کننده شامل اسیدهای تک یا پلی کربوکسیلیک غیراشباع و استرهای آنها است و ممکن است با فرمول کلی زیر نشان داده شود: ##EQU1## که در آن R1 و R2 یکسان یا متفاوت هستند و از گروه متشکل از H انتخاب می شوند. , CH 3 , C 2 H 5 , COOR 5 , CH 2 COOR 5 , CN, Cl and CONH 2 ; R 3 H، CH 3 ، C 2 H 5 ، COOR 5 یا CH 2 COOR 5 است . R4 H ، CH3 ، C2H5 یا C3H7 است . و R 5 H، CH 3 ، C 2 H 5 ، C 3 H 7 ، C 4 H 9 یا C 6 H 5 است . بنابراین، به عنوان مثال، اسید اکریلیک، متاکریلیک اسید، اسید کروتونیک، اسید مالئیک، اسید تیگلیک، مونو متیل مالئات، دی متیل مالئات، اسید فوماریک، مونو متیل فومارات، دی متیل فومارات، اسید ایتاکنیک، مونو متیل ایتاکنات، اسید مزاکونیک، اسید سیتراکونیک اسید مونو آمید و مالیک ممکن است مطابق با اختراع حاضر استفاده شود. دسته دوم از عوامل کربوکسیله کننده شامل انیدریدهای دی کربوکسیلیک دی کربوکسیلیک غیراشباع α، β و انیدریدهای مونوآمیدهای اسید دی کربوکسیلیک غیراشباع α، β است که ممکن است با فرمول های کلی زیر نمایش داده شوند: ##EQU2## که در آن R1 و R2 عبارتند از یکسان یا متفاوت و از گروه متشکل از H، CH 3 ، C 2 H 5 ، Cl و CN انتخاب شده است. R3 H، CH3 ، CONH است2 یا C 6 H 5 ; R 4 و R 5 یکسان یا متفاوت هستند و از گروه متشکل از H، CH 3 و C 2 H 5 انتخاب شده اند . بنابراین، انیدرید مالئیک، انیدرید ایتاکونیک، انیدرید سیتراکون، مالیمید و N-متیل مالیمید را می توان به عنوان عوامل کربوکسیله کننده نمونه در این دسته ذکر کرد. دسته سوم شامل کلریدهای اسید غیراشباع α، β است که با فرمول کلی زیر نشان داده می شود: ##EQU3## که در آن R1 و R2 یکسان یا متفاوت هستند و از گروه متشکل از H، CH3، C2 انتخاب می شوند . H 5 ، COOR 4 ، CH 2 COOR 4 ، CN، Cl، CONH 2 و COCl. R3 H ، CH3 ، C2H5 یا COOR4 است . R 4 H، CH 3 ، C 2 H 5 ، C 3 H 7 یا C 6 H 5 است . بر این اساس، کلرید اسید اکریلیک، کلرید متاکریلیک اسید، دی کلرید اسید مالئیک، کلرید اسید ایتاکونیک، کلرید اسید کروتونیک و غیره را می توان به عنوان مثال ذکر کرد. دسته چهارم شامل ترکیبات آلیلی حاوی کربوکسیل مانند اسید آلیل سوسینیک، آلی سوسینیک انیدرید و مانند آن است. دسته پنجم شامل ترکیباتی است که بر خلاف ترکیباتی که تاکنون ذکر شد، حاوی پیوند دوگانه غیراشباع نیستند، اما قادر به انجام واکنش های افزودن با IR و بر این اساس، قادر به وارد کردن یک گروه کربوکسیل یا گروه های کربوکسیل به IR هستند. بنابراین می توان به تیوگلیکولیک اسید، استرهای تیوگلیکولیک اسید، آزودی کربوکسیلیک اسید، استرهای آزودی کربوکسیلیک اسید و … اشاره کرد. عوامل کربوکسیله کننده فوق الذکر ممکن است به تنهایی یا در ترکیب یا در مخلوط با مونومرهای وینیل مانند استایرن، آکریل آمید، متیل متاکریلات و موارد مشابه استفاده شوند.
در عمل این اختراع، از ترکیبات اسید مالئیک به عنوان عوامل کربوکسیله کننده استفاده می شود. اصطلاح “ترکیبات اسید مالئیک” همانطور که در اینجا به کار می رود نه تنها شامل اسید مالئیک در معنای دقیق این اصطلاح می شود، بلکه مشتقات اسید مالئیک مانند انیدرید مالئیک، استرهای مونو یا دی آلکیل اسید مالئیک را نیز شامل می شود که باقیمانده های آلکیل استر آنها حاوی 1 تا 4 اتم کربن، انیدریدهای مونو یا دی آلکیل است که بخش های آلکیل آن شامل 1 تا 4 اتم کربن، مالیمید، مالیمید جایگزین شده با گروه های آلکیل 1 تا 4 اتم کربن و ترکیبات مشابه است.
تولید IR اصلاح شده توسط واکنش IR با یک عامل کربوکسیله کننده به طور خلاصه در زیر توضیح داده خواهد شد، اگرچه فرآیند تولید IR اصلاح شده هیچ بخشی از این اختراع را تشکیل نمی دهد. یک فرآیند معمولی شامل افزودن یک عامل کربوکسیله کننده به محلول IR و حرارت دادن مخلوط در دمای 50 تا 250 درجه سانتیگراد است. در یک جو گازی بی اثر به عنوان حلال برای IR، هر یک از موارد زیر ممکن است مورد استفاده قرار گیرد: هیدروکربن های آلیفاتیک و آلی حلقوی، به عنوان مثال، n-بوتان، ایزوبوتان، ایزوپنتان، n-هگزان، ایزواکتان، سیکلوهگزان، متیل سیکلوهگزان، و غیره. و هیدروکربن های معطر، به عنوان مثال، بنزن، تولوئن، زایلن، اتیل بنزن، و غیره. حلال های هیدروکربنی آلیفاتیک و آلی حلقوی ترجیحی آنهایی هستند که دارای 4 تا 10 اتم کربن و هیدروکربن های آروماتیک ترجیحی دارای 6 تا 12 اتم کربن هستند. در صورت لزوم، در انجام واکنش در محلول، ممکن است از یک آغازگر رادیکال (کاتالیزوری که رادیکال های آزاد را آزاد می کند) استفاده شود، مانند، به عنوان مثال، بنزوئیل پراکسید، آزوبی سیزوبوتیرونیتریل، دی ایزوپروپیل بنزن هیدروپراکسید، دی-تی-بوتیل پراکسید، هیدروپراکسید کومن. ، دی کومیل پراکسید یا مانند آن. یک روش جایگزین شامل تماس مادون قرمز جامد با یک عامل کربوکسیله کننده در طول جویدن IR با استفاده از رول یا مخلوط کن مانند مخلوط کن Banbury است. در این روش، یک آغازگر رادیکال نیز ممکن است به کار گرفته شود. محتوای cis-1،4 IR شروع معمولاً کمتر از 80 درصد و برای بهترین نتایج، کمتر از 95 درصد نیست. علاوه بر این، مادون قرمز اولیه ترجیحا دارای وزن مولکولی بالایی است که مربوط به ویسکوزیته ذاتی حداقل 3.0 دسی لیتر در گرم است که در تولوئن در دمای 25 درجه سانتی گراد اندازه گیری می شود. مطابق با اختراع فوری، محتوای کربوکسیل IR اصلاحشده بهطور مطلوب در محدوده 0.03 تا 20 و ترجیحاً از 0.05 تا 2 از نظر تعداد گروههای کربوکسیل در هر 100 واحد تکرارشونده مونومر ایزوپرن IR است. محتوای کربوکسیل زیر محدوده فوق بهبود قابل ملاحظه ای در پایداری مکانیکی، استحکام ژل مرطوب و استحکام لایه خشک ایجاد نمی کند، در حالی که محتوای کربوکسیل بیش از محدوده فوق منجر به افزایش بیش از حد ویسکوزیته لاتکس و محصولات لاستیکی ولکانیزه نهایی می شود. که بیش از حد سخت هستند اصطلاح “محتوای کربوکسیل” IR اصلاح شده همانطور که در سراسر این مشخصات استفاده می شود به معنی تعداد گروه های کربوکسیل در لاستیک مذکور است که به شکل ذرات ریز در لاتکس حاصل پراکنده شده اند. محتوای کربوکسیل با روش زیر تعیین می شود: IR اصلاح شده جدا شده توسط انعقاد لاتکس در بنزن حل می شود و گروه های کربوکسیل با محلول هیدروکسید سدیم در متانول بنزن (1:4 حجمی) با استفاده از برموتیمول بلو یا فنل فتالئین تیتر می شوند. یک شاخص گروههای کربوکسیل آزاد و گروههای کربوکسیل به شکل نمک از این طریق به صورت کمی تعیین میشوند.محتوای کربوکسیل IR اصلاح شده را می توان با تغییر شرایط واکنش مانند مقدار عامل کربوکسیله کننده با IR، مقدار آغازگر رادیکال و دمای واکنش کنترل کرد.
محلول IR اصلاح شده برای استفاده در روش امولسیون کردن ممکن است، زمانی که واکنش IR و عامل کربوکسیله کننده در محلول انجام شده است، مخلوط واکنش باشد. مخلوط واکنش ترجیحاً قبل از امولسیون شدن با آب شسته می شود تا هر عامل کربوکسیله کننده واکنش نداده حذف شود. هنگامی که IR اصلاح شده از واکنش IR جامد و عامل کربوکسیله کننده به دست می آید، و همچنین زمانی که مایل به انتقال IR اصلاح شده در مخلوط واکنش محلول به یک حلال جداگانه است، از یک حلال برای تهیه محلول IR اصلاح شده فوق استفاده می شود. در تهیه لاتکس استفاده شود. حلال فوق ممکن است هر حلالی باشد که قادر به حل کردن IR باشد و حلال مورد استفاده برای واکنش IR با عامل کربوکسیله کننده در محلول می تواند به صورت سودمند مورد استفاده قرار گیرد. حلال فوق ممکن است علاوه بر این، حاوی نسبت کمی از یک غیر حلال یا غیر حلال های IR یا IR اصلاح شده مانند متانول، اتانول و موارد مشابه باشد. غلظت معمول IR اصلاح شده در محلول 4 تا 20 درصد وزنی و ترجیحاً 5 تا 15 درصد وزنی است. مطابق با اختراع، بهترین نتایج با استفاده از محلول IR اصلاح شده حاوی مالئیک انیدرید متصل به نسبت 0.03 تا 2 گروه کربوکسیل در هر 100 واحد تکرارشونده مونومر ایزوپرن به دست می آید. چنین IR اصلاح شده با واکنش انیدرید مالئیک با IR در محلول همانطور که در اینجا در بالا توضیح داده شد، بدست می آید.
در مورد عامل امولسیون کننده مورد استفاده در امولسیون سازی محلول IR اصلاح شده، عوامل فعال سطح آنیونی که معمولاً در واکنش های امولسیون پلیمریزاسیون به کار می روند، مانند اولئات پتاسیم، نمک پتاسیم اسید رزین، پتاسیم آبیتات، آمونیوم. اولئات و غیره نتایج رضایت بخشی را ارائه می دهند. سایر سورفکتانتهای آنیونی مانند نمکهای پتاسیم یا سدیم اسید پالمیتیک، اسید استئاریک، اسید لوریک، اسید میریستیک و غیره، و نمک پتاسیم یا سدیم اسیدهای آلکیل بنزن سولفونیک نیز ممکن است مورد استفاده قرار گیرند. سورفکتانت های آنیونی ممکن است در ترکیب با سورفکتانت های غیر یونی استفاده شوند. به منظور دستیابی به خواص فیزیکی مطلوب محصول لاتکس، مقدار ماده امولسیون کننده به طور مطلوب 2 تا 20 قسمت وزنی و ترجیحاً برای بهترین نتیجه، 5 تا 12 قسمت وزنی در هر 100 قسمت وزنی IR اصلاح شده است. امولسیون سازی عموماً با هم زدن محلول IR اصلاح شده همراه با آب حاوی عامل امولسیون کننده مذکور انجام می شود و از آنجایی که امولسیون حاصل و لاتکس حاصل از آن در شرایط قلیایی بین pH 8 و pH 13.5 پایدار است، ممکن است قبلاً به امولسیون کننده آب اضافه شود. مخلوط عامل یک تنظیم کننده pH مانند هیدروکسید سدیم، هیدروکسید پتاسیم یا موارد مشابه. نسبت حجمی محلول IR اصلاحشده به آب در امولسیونسازی عموماً در محدوده 3:1 تا 1:10 است، اگرچه آب ممکن است در نسبتهای کمی بیشتر وجود داشته باشد. به منظور ارتقای پایداری لاتکس حاصل و ملاحظات اقتصادی، امولسیون سازی به طور مطلوب در نسبت محلول به آب IR اصلاح شده 3:1 تا 2:1.5 انجام می شود. امولسیون سازی با استفاده از یک دستگاه اختلاط معمولی مانند همومیکسر اپن باخ، آسیاب کلوئیدی، هموژنایزر، آسیاب پراکنده، میکسر خط یا دستگاه امولسیون سازی اولتراسونیک انجام می شود. اندازه ذرات مادون قرمز اصلاح شده که در لاتکس حاصل پراکنده شده است، با شرایط امولسیون مانند مقدار عامل امولسیون کننده و آب، و همچنین شدت هم زدن تعیین می شود.
روش حذف حلال از امولسیون روغن در آب حاصل ممکن است یکی از روشهایی باشد که معمولاً در هنر قبلی مورد استفاده قرار میگرفت و به ویژه تقطیر با بخار، تقطیر تحت فشار کاهشیافته، تقطیر با بخار تحت فشار کاهش یافته و غیره قابل قبول هستند. در صورت لزوم، لاتکس رقیق به دست آمده را می توان (با حذف جزئی آب) با هر روش معمولی مانند سانتریفیوژ کردن، خامه زدن و تبخیر تحت حرارت تغلیظ کرد. لاتکس حاصل زمانی به محصولات شکلی تبدیل می شود که میزان کل مواد جامد لاتکس به محدوده 1/0 تا 70 درصد وزنی برسد.
هنگامی که عامل کربوکسیله کننده با IR حاوی یک گروه قابل تبدیل، به عنوان مثال، از طریق هیدرولیز، به یک گروه کربوکسیل آزاد (یا نمک آن) مانند، به عنوان مثال، یک گروه انیدرید اسید یا گروه استر باشد، مرحله امولسیون سازی فوق الذکر و / یا مرحله جداسازی حلال یک IR اصلاح شده با گروه های کربوکسیل آزاد یا نمک آن را به دست می دهد. در عمل اختراع حاضر ضروری نیست که تمام اجزای لاستیکی موجود در لاتکس یک IR اصلاح شده حاوی کربوکسیل باشد. به طور کلی، ترکیبی از IR اصلاح شده و IR معمولی (تغییر نشده) برای تولید لاتکس استفاده می شود. در این رابطه، عواملی که در اینجا برای دستیابی به لاتکس بهبودیافته ضروری است و همچنین مواردی که در ادامه به آنها اشاره خواهد شد، مانند محتوای کربوکسیل و محتوای ژل IR اصلاح شده، اندازه ذرات لاتکس و غیره عبارتند از. همه مربوط و مربوط به مخلوط فوق نیز هستند. بنابراین، نتیجه می شود که IR اصلاح شده در زمینه این اختراع شامل IR اصلاح شده و مخلوطی از IR اصلاح شده با IR معمولی است. IR اصلاح نشده در مخلوط های مذکور ممکن است تا 80 درصد وزنی را تشکیل دهد.
بنابراین لاتکس شواهدی را ایجاد کرد که به طور قابل توجهی پایداری مکانیکی، استحکام ژل مرطوب و استحکام لایه خشک را نسبت به لاتکس IR معمولی بهبود می بخشد. با این حال، هنگامی که IR اصلاح شده استفاده شده دارای محتوای ژل نسبتاً بالایی باشد، ممکن است پایداری لاتکس تحت تأثیر نامطلوب قرار گیرد. وجود ژل در مادون قرمز اصلاح شده از این جهت مطلوب است که لاتکس استحکام ژل مرطوب و استحکام لایه خشک بالایی را نشان می دهد، اما از نظر پایداری مکانیکی نامطلوب است. محتوای ژل IR به طور کلی با معرفی گروه های کربوکسیل به زنجیره IR افزایش می یابد. بنابراین، تا آنجا که به تولید تجاری مربوط می شود، تهیه لاتکسی که اجازه حضور مقدار نسبتاً زیادی ژل در IR اصلاح شده را می دهد و در عین حال پایداری مکانیکی بهبود یافته را حفظ می کند، مطلوب است.
با توجه به اختراع مشخص شد که مشکل فوق الذکر می تواند با از پیش انتخاب تعادل مناسب بین محتوای ژل مادون قرمز اصلاح شده و اندازه ذرات لاتکس برطرف شود. به طور خاص، اگر قطر متوسط ذرات موجود در لاتکس حدود 0.2 تا 5μ باشد و محتوای ژل IR اصلاح شده در ذرات حداقل 5 درصد وزنی بر اساس وزن ذرات باشد، لاتکس IR اصلاح شده فوق، پایداری مکانیکی عالی نشان خواهد داد. لاستیک و نه بیشتر از مقدار محاسبه شده توسط فرمول زیر: 100- 2.17 (متوسط قطر ذرات – 0.2) 2 . به عنوان مثال، زمانی که میانگین قطر ذرات لاتکس تقریباً 0.2μ باشد، جزء لاستیکی موجود در ذره ممکن است حاوی ژل (قسمت نامحلول تولوئن) در محدوده ای تا حدود 100 درصد وزنی باشد و لاتکس بسیار پایدار می ماند. هنگامی که قطر متوسط ذرات لاتکس 5μ باشد، لاستیک موجود در ذرات ممکن است حاوی حدود 50 درصد وزنی بخش نامحلول تولوئن مطابق فرمول: 100-2.17(5-0.2) 2 باشد .
از توضیحات فوق مشخص خواهد شد که با کنترل محتوای ژل لاستیک در ذرات با توجه به اندازه ذرات لاستیک در لاتکس یا برعکس، با کنترل اندازه ذرات لاتکس با توجه به محتوای ژل لاستیک. در ذرات لاتکس، پایداری بالای لاتکس را می توان تضمین کرد، حتی اگر محتوای ژل به اندازه 100 درصد باشد یا اندازه ذرات لاستیک در لاتکس به اندازه 5μ باشد.
در سراسر این مشخصات و ادعاهای ضمیمه شده به آن، اصطلاحات “ژل” یا “بخش نامحلول در تولوئن” به عنوان رسوب در تولوئن تعریف می شود که از ریختن لاتکس در مقدار زیادی متانول برای انعقاد، با افزودن 1 گرم به دست می آید. از لاستیک در حاصل منعقد ذرات لاتکس به 100 سی سی. تولوئن، و سپس مخلوط تشکیل شده را به سانتریفیوژ در 7000 G (G: ثابت گرانشی) در دمای 25 درجه سانتیگراد قرار دهید. به مدت 30 دقیقه رسوب وزن شده و بر حسب درصد وزنی نسبت به وزن لاستیک موجود در مخلوط فوق بیان می شود.
در لاتکس طبق اختراع، اگر محتوای قسمت نامحلول تولوئن کمتر از 5 درصد وزنی باشد، استحکام ژل مرطوب و استحکام لایه خشک لاتکس از نظر تجاری قابل قبول نخواهد بود. مشخص شده است که لاتکسی که محتوایی از بخش نامحلول در تولوئن کمتر از 15 درصد وزنی دارد، رضایت بخش است. پایداری لاتکس زمانی کاهش می یابد که IR اصلاح شده دارای محتوای نامحلول تولوئن (ژل) بیش از مقدار داده شده توسط فرمول فوق با در نظر گرفتن اندازه ذرات لاتکس باشد. کاهش محتوای ژل مادون قرمز اصلاحشده، تهیه لاتکس با اندازه ذرات بزرگ را امکانپذیر میسازد. IR اصلاح شده با محتوای ژل کم را می توان به دست آورد، به عنوان مثال، با روشی که در آن IR با یک عامل کربوکسیله کننده در محلول واکنش می دهد و نسبت کمی از مونومر ایزوپرن یا آب اضافه می شود یا با روشی که در آن از یک هیدروکربن آروماتیک به عنوان ماده استفاده می شود. محیط واکنش اگر لاتکس از نظر مکانیکی پایدار باشد و اندازه ذرات آن بزرگ باشد، میتوان مقدار ماده امولسیونکننده مورد نیاز برای پراکندگی لاستیک را تا حد زیادی کاهش داد و بر این اساس، خواص فیزیکی لاتکس حاصل را بهبود بخشید. علاوه بر این، اندازه ذرات بزرگ باعث افزایش غلظت لاتکس، کاهش ویسکوزیته لاتکس و بهبود کارایی تغلیظ لاتکس می شود. از سوی دیگر، زمانی که ویژگیهای استحکام بسیار بالا لاتکس برای کاربردهای خاص مورد نیاز است، یک لاتکس با اندازه ذرات نسبتاً کوچک بر اساس یک IR اصلاحشده با محتوای ژل بالا برای چنین کاربردهایی ایدهآل است.
لاتکس طبق این اختراع مطلوب است به گونه ای که قطر ذرات IR اصلاح شده پراکنده در آن در محدوده 0.2 تا 5μ و ترجیحاً در محدوده 0.7 تا 4μ باشد. هنگامی که قطر ذرات بیش از 5μ باشد، مشخص شده است که حفظ پایداری لاتکس دشوار است حتی اگر محتوای ژل IR اصلاح شده بسیار کم باشد. استفاده از مادون قرمز اصلاح شده با اندازه ذرات کمتر از 0.2μ در اختراع حاضر از آنجایی که استحکام ژل مرطوب و استحکام لایه خشک بسیار بهبود یافته است، و پایداری مکانیکی و حرارتی عالی لاتکس مربوط می شود، در اختراع حاضر مورد نظر نیست. برای لاتکس IR معمولی یا سایر انواع لاتکس مفید است.
با توجه به اختراع حاضر، حتی زمانی که IR اصلاح شده دارای محتوای ژل بیش از 60 درصد وزنی یا حتی بیش از 70 درصد وزنی باشد، می توان لاتکسی با پایداری عالی به دست آورد. به ویژه باید تأکید شود که این تنها زمانی امکان پذیر است که رابطه بین قطر متوسط ذرات لاستیک پراکنده در لاتکس و محتوای بخش نامحلول تولوئن لاستیک در ذرات مذکور همانطور که در بالا تعریف شده است و روش هایی که قبلاً برای آماده سازی اصلاح شده شرح داده شده است امکان پذیر است. IR، امولسیون و/یا لاتکس در این زمینه بسیار مهم نیستند.
ویژگیهای استحکام بهبود یافته و پایداری عالی لاتکس طبق اختراع از نمونههای کاری که در ادامه توضیح داده میشود، بهتر درک خواهد شد. با این حال، به طور کلی باید توجه داشت که استحکام ژل مرطوب و استحکام لایه خشک لاتکس مطابق با اختراع با مقادیر استحکام مربوطه به دست آمده با لاتکس طبیعی یا بیشتر از آن است و لاتکس اختراع پایداری عالی را در طول مدت نشان می دهد. غلظت و سایر پارامترهای فرآیند از جمله این واقعیت که افزودن ترکیبات مرسوم مختلف مانند گوگرد، شتاب دهنده ها، اکسید روی و غیره از پایداری لاتکس یا محصولات حاصل کم نمی کند. بنابراین، لاتکس اختراع را می توان به راحتی در محصولاتی مانند دستکش های لاستیکی، محصولات پزشکی و بهداشتی و غیره پردازش کرد که در آنها توری های IR اصلاح نشده مانند Cariflex IR-700 (علامت تجاری ثبت شده شرکت نفت شل) را پردازش می کند. ثابت کرده اند دشوار است. بنابراین، در عمل، لاتکس این اختراع ممکن است به نحو مطلوبی با لاتکس های دیگر مانند لاتکس طبیعی، لاتکس IR معمولی، لاتکس کوپلیمر استایرن- بوتادین، لاتکس کوپلیمر اکریلونیتریل- بوتادین، لاتکس پلی بوتادین و لاتکس کلروپرن ترکیب شود تا ویژگی های حاصل از این قبیل بهبود یابد. توری های دیگر نسبت لاتکس اختراع حاضر به دیگر لاتکس بسته به محتویات جامد متفاوت است، اما ممکن است تا 10/90، ترجیحا بیشتر از 50/50 وزنی باشد.
در مثالهایی که در ادامه توضیح داده میشوند، اصطلاحات فهرستشده در زیر دارای معانی تعریفشده زیر هستند:
1. PHR: قطعات وزنی در هر 100 قسمت وزنی IR.
2. محتوای کربوکسیل IR اصلاح شده: همانطور که در بالا تعریف شد.
3. پایداری مکانیکی: مقدار انعقاد تشکیل شده در سانتریفیوژ لاتکس بر حسب درصد وزنی بر اساس وزن کل جامدات بیان می شود. یک تستر پایداری مکانیکی از نوع Maron استفاده می شود. شرایط اندازه گیری: بار 10 کیلوگرم. زمان 10 دقیقه؛ مقدار به دست آمده با پایداری لاتکس نسبت معکوس دارد، یعنی مقدار کم نشان دهنده پایداری بالا است.
4. استحکام کششی ژل مرطوب: لاتکس روی یک صفحه نگهدارنده پوشانده می شود، که سپس در محلول متانولی 30 درصد نیترات کلسیم در دمای 20 درجه سانتی گراد غوطه ور می شود. به مدت 3 دقیقه لاتکس منعقد شده به دست آمده در رطوبت نسبی 60 درصد و دمای 20 درجه سانتیگراد اجازه داده می شود تا خشک شود. به مدت 30 دقیقه پس از آن، استحکام نمونه با سرعت هد متقاطع 5 سانتی متر در دقیقه اندازه گیری می شود. در 25 درجه سانتی گراد
5. استحکام کششی فیلم خشک یا ژل خشک: سرعت متقاطع 5 سانتی متر در دقیقه.
6. محتوای نامحلول تولوئن (محتوای بخش نامحلول تولوئن): همانطور که در بالا تعریف شده است.
7. عدد متوسط قطر ذرات: ذرات لاتکس با اسید اسمیک (OsO 4 ) ثابت می شوند و قطرها با میکروسکوپ الکترونی اندازه گیری می شوند.
مثالهای زیر صرفاً نشاندهنده برخی از تجسمهای ترجیحی اختراع هستند و با توجه به دامنه اختراع که توسط ادعاهای پیوست شده در اینجا تعریف شده است، محدود نیستند:
مثال 1
Cis-1،4-polyisoprene با محتوای cis-1،4 98٪ و ویسکوزیته ذاتی [ν] 4.5 (dl/g) اندازه گیری شده در تولوئن در دمای 30 درجه سانتی گراد، که قبلاً با پلیمریزاسیون محلول تهیه شده بود. ایزوپرن در حضور یک کاتالیزور از نوع Ziegler، به عنوان IR شروع استفاده شد.
در 7 لیتر تولوئن 210 گرم حل شد. از IR فوق و سپس انیدرید مالئیک (به اختصار MAn) و بنزوئیل پراکسید (به اختصار BPO) در سطوح نشان داده شده در جدول 1 در زیر به محلول حاصل اضافه شدند. در اتمسفر نیتروژن، مخلوط در 100 درجه سانتیگراد حرارت داده شد. به مدت 3 ساعت، با هم زدن مداوم. سپس مخلوط واکنش در مقدار زیادی استون ریخته شد تا پلیمر رسوب کند، که سپس برای به دست آوردن یک IR اصلاح شده خشک شد (در جدول 1، نمونه های A تا G).
در 1 لیتر 80 گرم بنزن به طور همگن حل شد. از IR اصلاح شده فوق. به این محلول 560 گرم اضافه شد. محلول آبی 1% اولئات پتاسیم که با هیدروکسید پتاسیم به pH 11.5 تنظیم شده بود و مخلوط به مدت 5 دقیقه در همومیکسر با سرعت 9000 دور در دقیقه امولسیون شد (مقدار امولسیفایر: 7 PHR). حلال از امولسیون حاصل در دمای 60 درجه سانتیگراد خارج شد. تحت فشار کاهش یافته برای به دست آوردن یک لاتکس رقیق. سپس این لاتکس رقیق در دمای 25 درجه سانتی گراد سانتریفیوژ شد. و 7000 دور در دقیقه، که در آن لاتکس غلیظ با محتوای جامد 65٪ به دست آمد.
نتایج با توجه به خواص لاتکس غلیظ فوق در جدول 1 نشان داده شده است. برای مقایسه، خواص یک لاتکس غلیظ مشتق شده از ماده اولیه فوق الذکر IR (کنترل 1) و خواص یک لاتکس لاستیک طبیعی [محتوای جامد 62٪ لاتکس هریسون (کنترل 2)]، که هر دو به روشی مشابه بالا تهیه شده اند، در جدول 1 نیز آورده شده است. از جدول مشاهده می شود که لاتکس IR اصلاح شده مطابق اختراع، پایداری مکانیکی به طور قابل توجهی بهبود یافته است، ژل مرطوب. استحکام و استحکام فیلم خشک
Shimis.alizadeh@gmail.com
آدرس:
مشهد، فکوری17، نبش لاله2، شرکت ویلاتوس
شماره های تماس:
2 پاسخ
عالی بود مرسی
عالی بودین.
پشتیبانی تمام وقت داشتین.
تبریک به شما و به ما